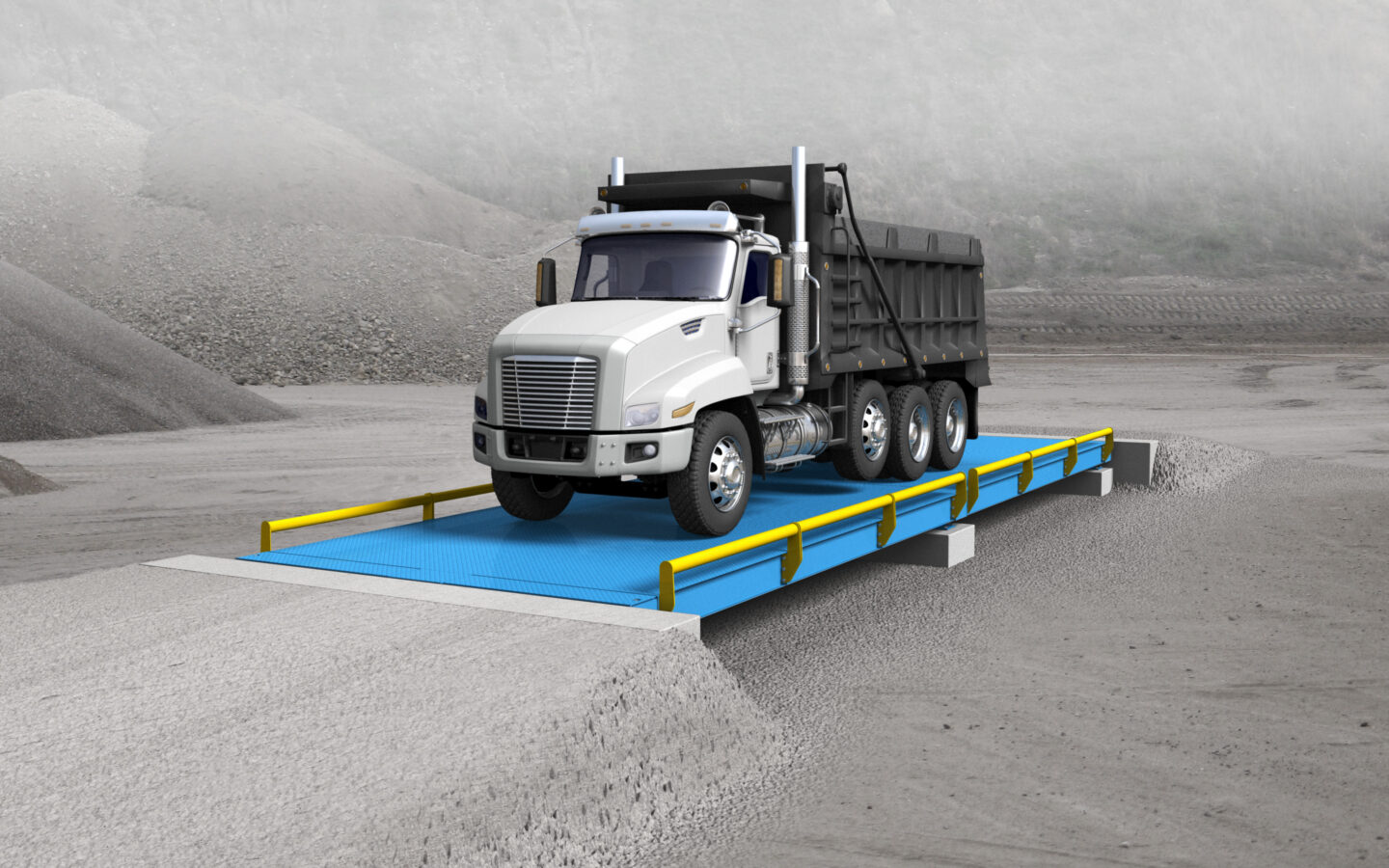
Logistics, warehouses, the food and beverage sectors, and even the pharmaceutical industry all rely heavily on scales. The selection of construction materials for scales is contingent upon their specific environmental requirements. For instance, basic certified scales in proximity often employ standard materials like plastic and painted carbon steel, whereas more demanding environmental conditions necessitate the utilization of stainless steels, commonly of AISI-304 or AISI-316 grade. The evaluation of a scale's accuracy is determined by several aspects, including but not limited to linearity, measurement uncertainty, resolution, and repeatability. Particularly in industries such as pharmaceuticals, the electropolishing of stainless-steel components is required to guarantee superior corrosion resistance and cleanliness.
Material Selection Process:
In essence, scales can be classified into two primary categories: basic scales and robust truck scales designed for harsh environmental conditions. Fundamental scales utilize materials like plastic, coated aluminum alloy, painted carbon steel, or galvanized steel.
Truck scales of this kind are primarily employed in weighing operations within logistics or warehousing settings. They operate in dry ambient conditions where hygiene and corrosion resistance are not of paramount importance. Temperature variations can range from room temperature to extremes (both high and low), and humidity levels can fluctuate significantly.
Stainless steels belonging to the AISI-304 and AISI-316 grades are the preferred choices for situations necessitating higher cleanability, chemical compatibility, and environmental stability. These austenitic stainless steels are equipped with a thin passive coating (metal oxide or metal hydroxide) that offers protection against oxidation and corrosion, safeguarding the metal from potentially corrosive chemicals in the working environment or samples.
Food and beverage, makeup, paint, pigment, and chemical-intensive businesses have all found that AISI-304 grade stainless steel works well for them. While it withstands chemicals present in products and cleaning agents, it may tarnish in the presence of highly abrasive chemicals.
For enhanced protection, the AISI-316F stainless steel is recommended. This material boasts superior resistance to pitting corrosion induced by potent chemicals like chlorides, salts, and acids due to its elevated nickel content and up to 3% additional molybdenum.
In cases requiring even greater protection, various sub-grades of AISI 316 stainless steel are available. Grade 316L, with lower carbon content for enhanced corrosion resistance, and grade 316Ti, featuring added titanium for increased tensile strength and resistance to inter-crystalline corrosion, are notable examples.
For critical applications such as pharmaceutical and medical technology manufacturing, electropolishing of AISI 304 or 316-grade stainless steels is essential to meet stringent standards for corrosion resistance and hygiene. Electropolishing significantly reduces surface roughness, making it difficult for germs to adhere to the metal.
The electropolishing process involves submerging a stainless-steel anodic workpiece in an electrolytic bath connected to the positive pole of a current generator. The cathode is linked to the negative pole, causing particles from the anodic workpiece to move to the cathode under electrical current.
Consequently, the workpiece's surface roughness diminishes, while its surface chromium concentration increases. The final surface has minimum roughness, which improves corrosion resistance and reduces microbiological contamination. The current benchmark is a roughness of 1 μm, though 0.8 μm and 0.4 μm are superior in terms of quality.
Ensuring Accuracy in Weighing:
Accuracy, a measurable aspect of measurement quality, has perpetually been a topic of discussion in the weighing industry. Multiple parameters interact to determine accuracy; among these, four quantifiable specifications play a pivotal role:
1.Linearity
Linearity pertains to the accuracy deviation (variance) of a truck scale's measurements across its entire weight range, encompassing both maximum and intermediate values. Reputed truck scale manufacturers and authorized service providers include a linearity test in their annual calibrations.
2.Measurement Uncertainty
The difference between a sample's measured weight and real weight, which is affected by elements like the weighing environment, is known as measurement uncertainty. Some applications closely monitor measurement uncertainty. For instance, the U.S. Pharmacopeia (USP) Chapter 41 specifies that measurement uncertainty during sample weighing should not exceed 0.1% of the weighed quantity. This standard is used by labs that use truck scales and is becoming more popular in manufacturing environments.
3.Resolution
The smallest change in mass that can be detected by a scale, referred to as its resolution or readability, is independent of the capacity of the scale. For example, a sample weighing 114.318 kg can be read as 114.318 kg on a scale with a precision of 0.001 kg and 114.32 kg on a scale with a resolution of 0.01 kg.
4.Reproducibility
Reproducibility characterizes a scale's ability to consistently yield similar results over time and when used by different users. A scale's repeatability is assessed by measuring a test weight ten times and calculating the standard deviation of these measurements. While many high-quality truck scales automate this process, manual computation is also feasible.
This in-depth piece about truck scales aims to supply readers with as much information as possible on the subject. The topic of material selection is discussed in depth, with an emphasis placed on stainless steel grades such as AISI-304 and AISI-316 to meet a variety of environmental conditions. The importance of electropolishing in attaining corrosion resistance and maintaining cleanliness is discussed in detail here.
The accuracy aspect is dissected through parameters like linearity, measurement uncertainty, resolution, and reproducibility. The purpose of this article is to provide readers with a thorough comprehension of truck scales and to encourage them to conduct extensive research before selecting an appropriate model and collaborating with truck scale manufacturers for installation.At Apollo Scales, we are proud to produce vehicle scales outfitted with cutting-edge hardware and software. Pioneers in the field have devised these innovations to satisfy the evolving requirements of lorry scale applications.